What is Bladder and Tubular Hydroforming?
Hydroforming is simply using the force of a liquid such as water, oil, or hydraulic fluids to shape a component. It is an affordable way of making ductile metals like brass, alloy steel, aluminum, stainless steel, etc. into different forms and shapes. Most metals that have the ability to cold-form can get hydro formed. This helps to make them strong and structurally stiff.
Hydroforming works as a type of specialized die forming. It utilizes high-pressure hydraulic liquids to press working materials that are at room temperature into a die. In this way, complex shapes which would ordinarily be impossible are formed without need for welding.
Hydroforming is used in a variety of industries most especially in the automobile and aerospace industries. These industries make use of these composite shapes to manufacture lighter, stronger as well as rigid one-piece structures. These structures are then used in manufacturing car and plane parts.
Hydroformed parts are often made with a greater stiffness-to-weight ratio and at a lower cost when compared to conventional methods. You can read further on this here. There are two main types of hydroforming. They are bladder and tubular.
Bladder Hydroforming
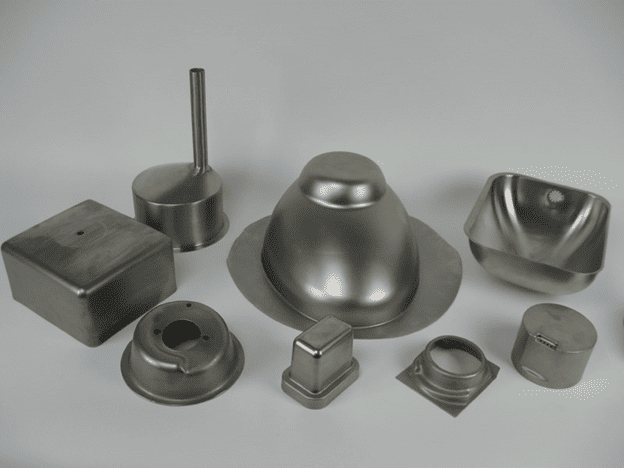
This is also known as sheet or deep draw hydroforming. In this process, a blank sheet of metal is placed in the press. Pressure is applied to this metal and this forces it into the die that is beneath it. This type of hydroforming is versatile and can be used for a broad range of parts.
This method is beneficial to several industries including healthcare, defense, aerospace, power generation and commercial lighting. All these fields need complex and specialized shapes as well as parts that must be adhered to strictly. Sheet hydroforming helps to provide the precise surfaces and shapes that are required.
In this type of method, there is bladder forming where in that bladder contains the fluid. Therefore, the liquid does not come in direct contact with the sheet. This type is quite similar to using stamping but a rubber diaphragm is used.
This diaphragm is supported by up to 18,000 psi of oil pressure and works as the other punch half. When this pressure is increased, it forces the metal into the press taking its shape. The tooling cost for this method is reduced in half because only one part of the die is needed.
The process starts with a blank sheet, a blank holder, a die as well as a punch. The blank piece is placed into the holder which is over the die. The die’s cavity is the shape of the part that is to be formed. The next step is the punch moves towards the sheet and pushes it into the die.
This stretches or bends the part into the required shape but does not alter the sheet’s strength. The shapes formed may be straight or may have different cross-sections, curved walls and so on. The most common though are rectangles and cylinders. Examples of these parts are cans, cups, fuel tanks, car frames, etc.
Tubular Hydroforming
Tubular hydroforming is so named because of the metal tubes utilized as the foundation for the formed part. It is a particularly useful process for the automotive industry as there is a great requirement for tubular parts.
In this process, pressurized fluid is used on the insides of the tube. This metal is pushed out into the mold that is surrounding it thereby getting its shape. This process is used to create a variety of tubing as well as pipes of different lengths, shapes and weights.
Stiffness, dimensional accuracy, as well as strength, are effortlessly achieved using this process. It also helps to make light and safe parts for the automobile industry.
Tubular hydroforming involves two main practices which are low pressure and high pressure. In the low pressure process, pressure is applied moderately to the tube when the die is closed. For the high pressure, the tube is totally enclosed in the die before pressure is applied.
The whole process starts with an idea of the part that is needed. Engineers and designers research and work to form a plan and ultimately produce a prototype. This prototype is then created using this hydroforming method. The process is labor-intensive but it produces very high quality, light and durable components.
It has also become increasingly popular for its history of producing these quality parts at a reduced cost. It is now commonly used in design, industry and innovation allowing automotive parts to be constructed easily. A good example is in the bicycle making industry. Due to this process, bicycles are lighter, more sturdy and agile than they have ever been.
Tubular hydroforming comes with benefits that include:
- Better flexibility in product design and strength
- Lighter weight due to using less material
- Greater bending strength and stiffness
- High level of accuracy in production
- Greater overall quality
Bladder vs Tubular
While bladder and tubular hydroforming are important, they are used to obtain different sets of results. Tubular is used when complex components like curved sections are needed. Examples of these include door handles of trucks, car parts, bicycle frames, brass tubes of saxophones, etc.
Bladder or sheet hydroforming on the other hand is used when large and flat components are required in a particular shape. Examples include car doors, antennas, lighting fixtures, etc. Between the two, there is no better option. The best method to use per time is dependent on what you desire to create.
Conclusion
Hydroforming was initially used for making kitchen spouts and plumbing fixtures. It has grown over the years and has become very popular in a variety of manufacturing industries. Its versatility makes it useful for making many different parts that are useful to these industries.
What’s more, it also comes with plenty of benefits. Chief amongst these is its affordability and the high quality of parts produced. Added to these, the components produced are sturdy and long-lasting. Of the two processes, the best to use depends on the project as well as the type of equipment available.